Guide from eTAZ Systems
Pressure measurement plays a key role in many areas, from industrial processes to healthcare. At eTAZ Systems, we offer reliable and accurate pressure measurement solutions designed to meet the needs of various industries such as oil and gas, manufacturing and healthcare. To ensure that systems operate efficiently and accurately, you should understand how to measure pressure.
What is pressure ?
Pressure is basically a force acting on a certain area. In technical terms, the amount of force exerted per unit area on the surface of an object defines pressure. We measure it in different units, such as pascals, bars, atmospheres (atm), or pounds per square inch (psi). Engineers and technicians use pressure measurement to control the movement of liquids, gases, or vapors, making it indispensable in many industrial processes.
How is pressure measured?
The principle of pressure measurement consists in detecting the force that a fluid (either gas or liquid) exerts on a surface and converting it into an electrical or mechanical signal.
There are three basic types of pressure measurement:
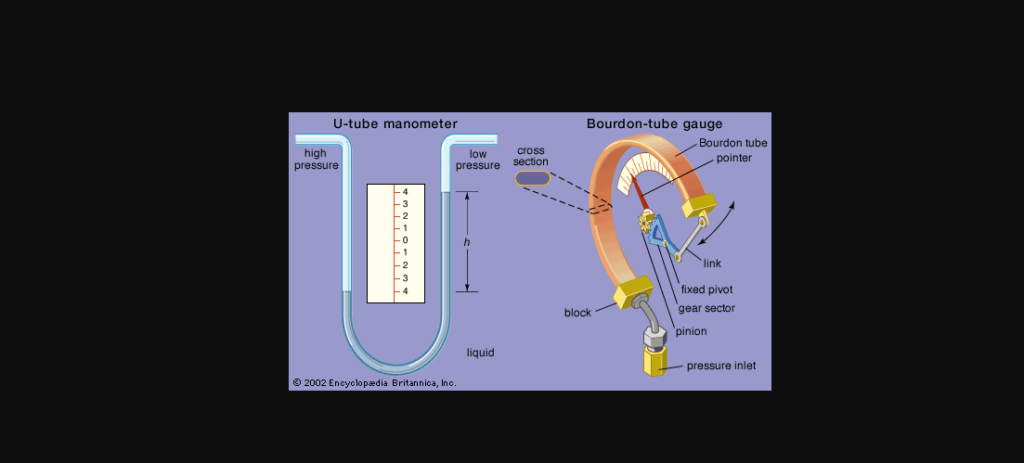
Absolute Pressure:
Pressure measured relative to a complete vacuum.
Overpressure:
Pressure measured relative to ambient atmospheric pressure.
Differential pressure:
The difference between two pressures in a system. Key pressure measurement technologies Mechanical pressure gauges Mechanical pressure gauges are simple and rely on components such as springs, diaphragms and tubes to measure pressure.
These gauges are robust and extensively utilized in challenging conditions
Bourdon tubes:
When you apply pressure, these curved tubes straighten and move a needle to indicate the pressure level. They cost less and are widely used in industry.
These indicators utilize a pliable membrane that distorts under pressure and transforms the distortion into a measurable reading.
They are ideal for low pressure measurements and work well with corrosive materials.
Manometers:
These are simple instruments that measure pressure based on the height difference between two columns of liquid (such as mercury or water). Scientists often use manometers in laboratory settings. Electronic pressure sensors convert pressure into an electrical signal that the system processes. These advanced sensors are commonly used for precise measurements.
Capacitive sensors:
These sensors work by changing the distance between the capacitor plates when pressure is applied and the change in capacitance is measured.
Piezoelectric sensors:
These generate a voltage when pressure is applied, making them ideal for applications requiring dynamic pressure measurement, such as motors.
Strain Gauges:
These sensors detect changes in resistance when pressure is applied, making them suitable for many general industrial applications.
Optical sensors:
Use light to measure pressure changes, which is particularly useful in environments where there is electrical interference.
Resonant sensors:
Resonant pressure sensors measure pressure based on frequency shifts of a vibrating element. They are highly accurate and used in critical applications such as the aerospace industry.
Calibration and accuracy Regular calibration is required to ensure accurate pressure measurement. Calibration adjusts sensors to match known standards under various conditions. This is particularly important in areas such as healthcare, pharmaceuticals and energy. Application of pressure measurement Industrial Process Control:
Pressure monitoring helps control processes such as chemical reactions and steam generation.
Healthcare:
Blood pressure monitors and ventilators depend on accurate pressure measurements. Aeronautics and Aviation:
Pressure sensors are used to control cabin pressure and altitude in an aircraft. HVAC systems:
These systems rely on pressure sensors to regulate air flow.
Automotive:
Tire pressure monitoring systems and engine pressure sensors help ensure safe vehicle operation. Obstacles in pressure detection
Pressure detection can be challenging in specific conditions.
Some of the challenges include:
Temperature changes: Extreme temperatures can affect the accuracy of the sensor. Corrosive media: Sensors exposed to chemicals can degrade over time. Dynamic pressure changes: Sensors in applications such as engines or explosions must respond quickly to fluctuating pressures.
Frequently asked questions from eTAZ Systems
1. What are the main types of pressure?
The main types are absolute, gauge and differential pressure.
2. How often should pressure sensors be calibrated?
Calibration depends on the industry. Fields requiring high accuracy, such as healthcare or aerospace, may necessitate yearly or more regular calibration.
3. What affects the accuracy of pressure measurement?
Factors such as temperature changes, improper calibration, and environmental conditions can affect accuracy.
4. Which kind of sensor is the most precise?
Resonant pressure sensors are highly accurate, but the choice depends on the specific needs of your application.
5. Can pressure sensors measure very low pressure?
Yes, sensors such as membrane or capacitive are intended for low-pressure measurements.
6. Are pressure sensors suitable for corrosive environments?
Yes, some sensors with a protective coating or made of materials such as stainless steel are resistant to corrosive environments.
7. What is the service life of the pressure sensor?
With proper care, industrial sensors can last 5 to 10 years or more.
Conclusion
Understanding how pressure is measured is critical to many industries.
At eTAZ Systems, we offer advanced pressure measurement solutions that ensure accuracy and reliability, whether you work in healthcare, aerospace or industrial automation. Contact us today to find out how we can optimize your pressure measurement systems!