S-type load cells are essential for measuring force and weight accurately in various industrial applications. eTAZ systems Understanding their working principle is crucial for ensuring their efficiency and accuracy. This blog post will delve into the core working principle of S-type load cells, their applications, integration challenges, technological advancements, and how to select the right one for your needs.
What Is an S-Type Load Cell and Its Applications
An S-type load cell, named for its characteristic “S” shape, is a critical sensor in accurately measuring force and weight. These devices play a pivotal role in both tension and compression load measurements. Their versatility finds them at the heart of various sectors, including industrial weighing setups, material testing apparatus, and crane scales, to name a few. This diverse applicability stems from their exceptional precision and dependability.
In industrial contexts, S-type load cells are integral to maintaining operational efficiency and safety. For example, material handling and processing industries ensure accurate measurement of loads to prevent equipment overloading. In testing and quality control, these load cells provide precise force measurements, enabling engineers to assess material strength and durability under different conditions. The aviation sector also relies on S-type load cells for weighing and balancing aircraft, ensuring load distributions meet safety standards.
Their unique shape facilitates easy installation in a variety of setups and allows for the measurement of both push and pull forces. This dual capability makes S-type load cells indispensable in sectors where precision and versatility in force measurement are paramount.
The Core Working Principle of S-Type Load Cells
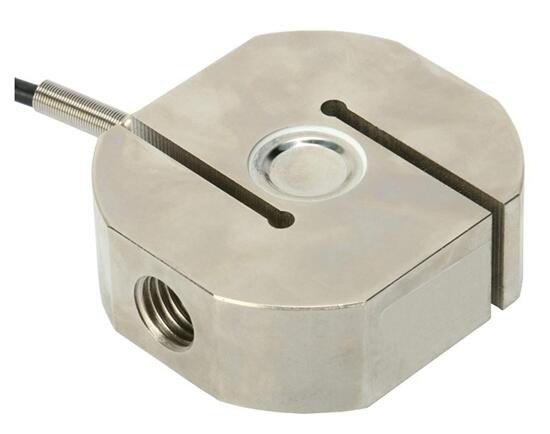
At the heart of an S-type load cell’s functionality is strain gauge technology’s innovative use. This technology is integral in transforming physical force into a measurable electrical output. Strain gauges within the load cell’s structure are precisely affixed to a bendable metal element. As force is exerted upon the load cell, this metal element deforms.Such deformation, albeit minute, significantly alters the electrical resistance of the strain gauges.
This change in resistance is not arbitrary but directly correlates with the magnitude of the force applied. The strain gauges connect in a Wheatstone bridge configuration, a circuit design specifically utilized for measuring electrical resistance changes with high accuracy. As the resistance changes, the Wheatstone bridge loses balance, leading to a measurable voltage difference across the bridge. This voltage difference, accurately calibrated, provides a direct representation of the force applied.
Consequently, the electrical signal output by the S-type load cell is proportional to the force exerted, whether in tension or compression. This proportional relationship allows for precise quantification of the applied force, translating physical stress into an electrical signal that can be easily measured and analyzed. This method offers S-type load cells a reliable means for assessing force and weight in many applications.
An Overview of eTAZ Systems and Their Relevance
TAZ systems, which are electronic torque and Z-weight measuring systems, integrate seamlessly with S-type load cells to broaden the scope of measurement capabilities beyond mere weight to include torque. These systems are pivotal in environments where the simultaneous assessment of both parameters is necessary for comprehensive analysis and control. Particularly prevalent in automotive testing and aerospace, eTAZ systems facilitate a level of precision in measurement that is indispensable for evaluating mechanical performance and adherence to stringent safety standards. In material handling, accurately gauging torque alongside weight allows for enhanced operational control, optimizing the efficiency and safety of equipment usage. The real-time data provided by eTAZ systems empowers engineers and technicians with actionable insights, enabling proactive adjustments and fostering an environment of continual improvement.
Integration Challenges and Solutions for S-Type Load Cell
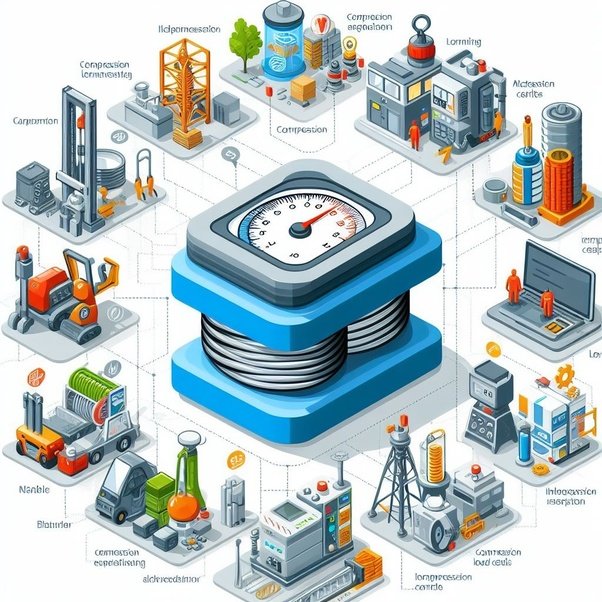
Integrating S-type load cells into various applications presents unique challenges that demand precise attention to detail to ensure optimal performance. A primary hurdle is the necessity for meticulous alignment and secure mounting to avoid skewed measurements, which can significantly detract from the system’s reliability. Inaccurate force application due to misalignment jeopardizes data accuracy and can prematurely wear the load cell, necessitating unexpected maintenance or replacement.
To surmount these obstacles, it’s crucial to employ specialized mounting hardware to facilitate correct positioning and absorb any extraneous forces that could impact the load cell’s performance. This hardware typically includes swivel mounts, load buttons, and rod end bearings, which aid in maintaining the correct load path and reducing side load effects.
Moreover, implementing a thorough calibration process upon installation and at regular intervals ensures that S-type load cells maintain high accuracy over their operational life. This calibration, often conducted with certified weights or through comparison methods, helps identify deviations from expected performance early on.
Environmental factors such as temperature fluctuations, humidity, and electrical noise can also affect the load cell’s function. Utilizing S-type load cells with built-in temperature compensation and electromagnetic interference (EMI) shielding can mitigate these issues, preserving the integrity of the measurements.
By addressing these integration challenges through appropriate mounting techniques, regular calibration, and considering environmental influences, users can enhance the performance and lifespan of S-type load cells in their applications.
Advancements in S-Type Load Cell Technology
“We have notably enhanced the precision of S-type load cells, allowing their use in more sensitive and demanding applications where minute force variations must be captured with high fidelity. One of the groundbreaking developments in this field is the introduction of wireless S-type load cells. These wireless variants offer a streamlined solution by eliminating the complexities associated with traditional wired systems, such as the need for extensive cable management and the risk of cable damage in harsh environments. This technological leap facilitates ease of installation, mobility, and adaptability in various operational contexts, from industrial settings to remote monitoring applications.
Integrating advanced signal processing algorithms represents another leap forward in enriching the S-type load cell’s capabilities. These algorithms enable more refined and accurate data analysis, effectively minimizing the impact of noise and other external factors that could compromise measurement accuracy. “We have notably enhanced the precision of S-type load cells, allowing their use in more sensitive and demanding applications where minute force variations must be captured with high fidelity.
Moreover, the advent of materials and manufacturing techniques has produced more durable and resilient load cells. These advancements extend the operational lifespan of S-type load cells and broaden their suitability for extreme conditions, including high humidity, temperature fluctuations, and corrosive environments. As a result, the modern S-type load cell embodies a fusion of robustness, precision, and technological sophistication, ready to meet the challenges of today’s dynamic measurement needs.
Selecting the Right S-Type Load Cell for Your Needs
Choosing the ideal S-type load cell requires carefully assessing various vital parameters to perfectly match your application’s demands. The load capacity is paramount; selecting an appropriate range of cells ensures accurate measurements without risking overloading. Accuracy is another critical factor, influenced by the environment in which the cell will operate and the precision level needed for your specific tasks. The conditions of the environment—whether it involves extreme temperatures, moisture, or potential corrosive substances—dictate the need for load cells designed with protective features or materials to withstand such challenges.
Compatibility with existing measurement or control systems is also essential, ensuring seamless integration and data collection. Engaging with manufacturers early in the selection process can provide valuable insights into the compatibility and potential customizations needed for your setup. Additionally, exploring the available certifications, such as those for hazardous environments, can be crucial depending on the application area. Taking these considerations into account helps pinpoint a load cell that meets your technical requirements and aligns with long-term reliability and support considerations.
FAQS
Q: How precise can S-type load cells be?
A: The precision of S-type load cells can vary, typically ranging between 0.1% and 0.5% of full-scale capacity. This variation is dependent upon the model and the device’s manufacturing standards.
Q: What’s the recommended calibration frequency for these load cells?
A: The recommended calibration frequency for S-type load cells is at least annually. However, more frequent calibration might be necessary for applications with heavy usage or in critical measuring conditions to ensure continued accuracy.
Q: Are S-type load cells suitable for use in environments with potential explosive risks?
“Yes, manufacturers specifically design certain models of S-type load cells to be safe for use in hazardous environments, including those with risks of explosive gases or dust. It is important to select a load cell certified for the specific dangerous environment where you will deploy it.