Have you ever wondered how load cells work? These innovative devices are crucial in various industries, eTAZ systems from manufacturing to aerospace. In this blog post, we will delve into the mechanism behind load cells and explore their functionality in more detail. So, how do load cells work?
Understanding the Basics of Load Cells
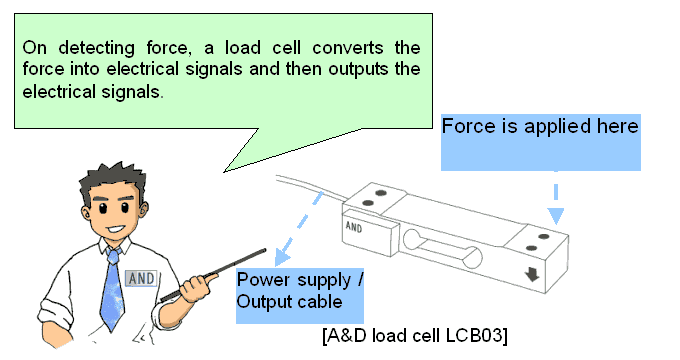
Load cells, at their core function, sophisticated devices designed to transduce or convert a physical force into a quantifiable electrical signal.
This fundamental process enables the precise measurement of weight or force exerted upon an object.
Load cells reflect their versatility through the vast array of forms tailored to meet the demands of specific applications.
These forms range from compact models ideal for high-precision tasks to robust units crafted for heavy industrial use.
Load cells, manufactured from durable materials like steel, aluminum, or alloy steel, withstand the rigors of their environments while maintaining accuracy.
. The choice of material impacts the device’s durability, sensitivity, and operational range, making the selection process critical to achieving the desired measurement outcomes.
Load cells’ adaptability allows them to be integrated into various systems, accommodating a broad spectrum of industrial requirements. This adaptability is further enhanced by the incorporation of different types of strain gauges, which are pivotal in converting mechanical force into electrical signals. Through this conversion process, load cells can offer precise, real-time measurements crucial for monitoring and controlling industrial processes. Their ability to accurately measure force or weight underpins their essential role across numerous sectors, illustrating their importance in modern industry.
The Physics Behind Load Cell Operation
The fundamental principle that allows load cells to function roots in the science of elasticity and electrical resistance, specifically how these properties interact under the application of force. The operational mechanism of a load cell comprises strain gauges, critical components that undergo deformation when force is applied.
This deformation is not arbitrary but rather a precise, controlled flex that occurs within the elastic limits of the material.
The load cell ensures that it returns to its original shape once the force is removed, maintaining its integrity and reliability over many use cycles.
The deformation of the strain gauges causes a measurable change in their electrical resistance.
The electrical resistance of a conductor changes when stretching or compressing causes this phenomenon to occur. The change is proportional to the force applied, allowing the load cell to transduce mechanical force into an electrical signal. The signal processes and converts into a voltage variation, which quantitatively relates to the force exerted on the load cell. Through this sophisticated interplay of physical and electrical principles, load cells provide a reliable and accurate means for measuring force, enabling widespread application across numerous fields.
Role of Strain Gauges in Load Cells
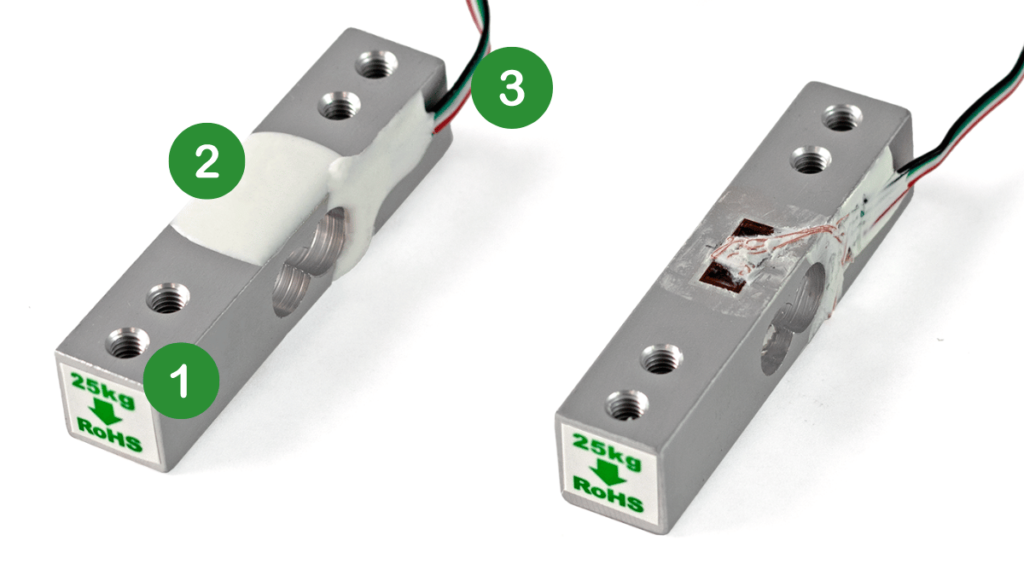
Strain gauges are indispensable to load cell functionality, serving as the primary sensing elements that detect and measure force and pressure. The application of force to a load cell causes the physical deformation of the strain gauge attached to it. This deformation leads to a change in the strain gauge’s electrical resistance, a phenomenon proportional to the force exerted. This change in resistance is ultimately responsible for the load cell’s ability to measure force accurately.
The load cell embeds strain gauges, meticulously aligning and bonding them to the structure in areas most susceptible to strain when force is applied.
The arrangement and quantity of strain gauges within a load cell can vary depending on the design and requirements of the measurement application. In a Wheatstone bridge arrangement, engineers typically configure them to precisely measure the resistance changes caused by strain. This setup enhances the sensitivity and accuracy of the load cell, allowing for detecting even minute changes in resistance due to force application.
The precise calibration and alignment of strain gauges within the load cell are critical for accurate force measurement. By responding to the mechanical deformation with a measurable change in the electrical signal, strain gauges bridge the gap between physical force and electronic measurement, enabling the load cell to function as an effective transducer.
Exploring eTAZ Systems and Their Integration with Load Cells
TAZ systems represent the forefront of load cell technology, blending traditional load cell mechanisms with cutting-edge electronic features to enhance measurement accuracy and user interaction.
Engineers design these systems to leverage the precision of load cells while introducing digital enhancements such as intuitive user interfaces, comprehensive data logging, and advanced analytics capabilities. Integrating eTAZ technology with load cells simplifies the process of monitoring and analyzing weight and force measurements and introduces a level of convenience and efficiency previously unattainable. By offering features like remote monitoring, eTAZ systems facilitate the real-time observation of measurements from any location, a significant advancement for industries requiring constant and precise monitoring. The adaptability of these systems allows for seamless integration into existing infrastructures, ensuring that industries ranging from manufacturing to healthcare can benefit from the enhanced capabilities of eTAZ systems without the need for extensive modificationsy.
Calibration and Accuracy in Load Cell Systems
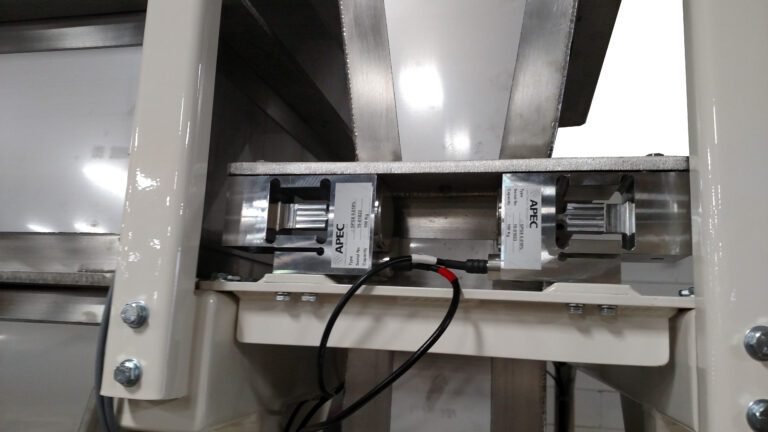
Ensuring the precision of load cells is paramount for their practical application across various sectors. Calibration emerges as a critical process in maintaining the integrity of measurements, serving as a systematic adjustment that aligns the load cell’s outputs with known standards. This process mitigates potential inaccuracies arising from environmental changes, mechanical wear, or shifts in measurement parameters over time.
Professional calibration involves subjecting load cells to known weights or forces and adjusting their output to match the applied standards accurately. This meticulous procedure not only verifies the load cell’s accuracy but also identifies any deviations from expected performance metrics. Meanwhile Professionals can achieve high measurement fidelity by utilizing specialized calibration equipment, ensuring that load cells operate within their specified accuracy range.
The frequency of calibration is dictated by the usage intensity, the critical nature of measurements, and regulatory standards specific to industries. Adherence to a regular calibration schedule is essential for industries where precision is non-negotiable, such as aerospace, automotive testing, and pharmaceutical manufacturing. Beyond maintaining accuracy, calibration also extends the lifespan of load cells by identifying and addressing potential issues before they escalate into significant malfunctions.
Through this rigour, calibration bolsters the reliability of load cells, underpinning the trust placed in these devices for critical measurements and analyses.
Applications of Load Cells in Industry
The versatility of load cells enables their widespread application across various industries, demonstrating their indispensability in everyday and specialized tasks. In material testing, load cells provide the critical data for evaluating the structural integrity and performance characteristics of various materials under different stress conditions. This information is vital for industries that demand high safety and quality standards, such as construction and automotive manufacturing.
In industrial automation, load cells play a central role in systems aimed at improving precision and efficiency. In assembly lines, packaging machinery, and robotics, they consistently transmit accurate weight measurements to optimize operational flow.
Furthermore, the healthcare sector benefits significantly from the precision of load cells, especially in medical devices that require the utmost accuracy in force and pressure measurement for patient care and diagnostic equipment.
Moreover, their applications extend to agriculture, where they monitor feed and grain weights; retail, where they provide scale systems; and even the aerospace industry, where they test the stress and strain on materials. Each application underscores load cells’ adaptability and essential nature, highlighting their critical role in advancing industry standards and technological innovation.
Conclusion
As we have explored, the function and significance of load cells span across many industries, To clarify marking them as fundamental instruments for precision measurement. The intricacies of their operation, grounded in the principles of physics and enhanced through technological advancements like eTAZ systems, showcase the dynamic evolution of these devices. From the core function of converting physical force into an electrical signal to the critical role of strain gauges in ensuring measurement accuracy, each aspect of a load cell’s design contributes to its reliability and efficiency. The continuous development and integration of digital technologies further cement the status of load cells as indispensable assets in industrial, healthcare, and research applications. Embracing regular calibration and understanding the application-specific requirements is crucial to leveraging the full potential of load cells.
Pingback: Circuit Design with eTAZ Systems -